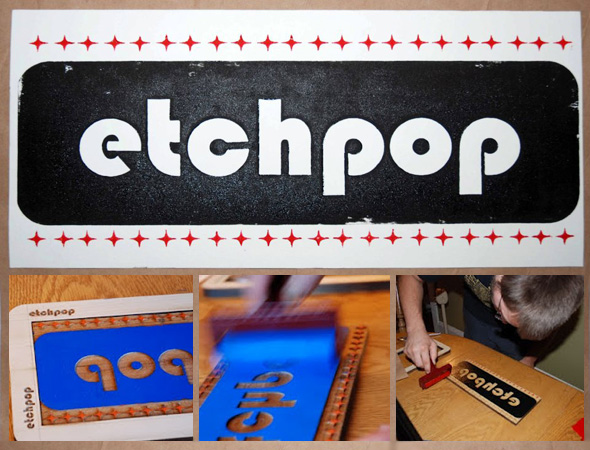
When your Kickstarter campaign raises more than double your original goal, you're probably onto something good. That's what happened with Portland-based startup Etchpop last year, and it's clear why they've been so successful: they have a completely simple, completely amazing idea.
With an official launch scheduled this month, Etchpop is a web-base service that allows you to design and order your own custom laser-etched woodblocks. Whip up whatever design you'd like, submit it to Etchpop and you'll receive a woodblock of that design to make handmade prints as you'd like.
How Etchpop works.Having taken out a small business loan to arm themselves with a Trotec laser (even before they launched their Kickstarter campaign), Etchpop's Marshall Tipton and Chester Lindgren have not been messing around. Already, they've put together a handy starter kit to get you printing, and Etchpop's new website--built by Subtext--promises to offer an easy and simple way to upload your designs and order woodblocks.
After encountering Etchpop's exciting and unique combation of cutting-edge technology and hands-on, DIY craftwork, we couldn't resist getting in touch to find out more. Check out our Q&A below.
3rd Ward's John Ruscher: How did you and Chester come up with the idea for Etchpop?
Etchpop's Marshall Tipton: For as long as we've known each other, we've always been dreaming up ideas for businesses or products that we could bring into world. Chester has always been a bit of the 'mad scientist' type, and myself a little more pragmatic so we compliment each other well. A little over a year ago Chester told me he had access to a laser cutting/engraving machine. The first thing that popped into my head was engraving an image into wood and printing it. I designed a birthday card for my dad and that was when we made our first laser engraved woodblock. The card was a hit. I actually used it for several of my friends and family members who had birthdays around that time. Everyone loved the card. A few weeks later Chester called me late at night, obviously in the midst of another mad scientist brainstorm, proposing the idea of a website where anyone can submit an image to be engraved into wood to make their own woodblock prints. After many months of deliberation and a few empty bottles of whiskey later, we decided to finally 'pull the trigger' on one of our crazy ideas.
An Etchpop laser-etched woodblock.JR: Did either of you have a background in printmaking?
MT: We both had very little direct experience with printmaking, but we had experienced it vicariously—Chester through his ex-girlfriend who majored in printmaking at PNCA (Pacific Northwest College of Art) and I through my wife who is an artist and my brother who is a graphic designer. However, instead of sitting on the couch in a jealous delirium, we started to nerd out on all things letter-press related, and two years later we feel fantastic.
JR: What has the Etchpop timeline been like?
MT: It's all been alarmingly fast. We came up with the idea in early 2011 and spent a few months ruminating how we might actually get this thing off the ground. By the end of spring, we had decided to turn to Kickstarter and began working on the video in the summer. We posted the video in October, and it's been a blur ever since.
The Etchpop starter kit.JR: What made you decide to use Kickstarter?
MT: We've always been a fan of Kickstarter and we love the platform it provides to help creative entrepreneurs get on their financial feet. It's a great way of finding out if there is a market for a new idea without having to spend a lot of money upfront. We are always emailing each other links to different Kickstarter videos to check out. It's a great source of inspiration to see all the amazing ideas people are funding and watching them come to fruition with the help of the community.
JR: Can you tell us a little about this Trotec laser that you bought?
MT: Trotec lasers are basically the Mercedes Benz in this class of laser machines. They are designed and built in Austria and have Synrad laser tubes that are manufactured in Washington State (just north of us). There are definitely many cheaper options but we wanted a high quality machine that is capable of production day-in and day-out, and Trotec is definitely it.
The founders of Etchpop.JR: How will the process of ordering a custom woodblock work?
MT: We will have some simple and playful tutorials to help people get their images ready for a woodblock application, but there will definitely be a lot of back and forth to make sure people's blocks turn out the way they should. As Etchpop grows we will be slowly building an image editor that will specifically meet the needs of our customer base, piece by piece as their needs become evident.
JR: Any tips or words of advice for would-be creative entrepreneurs?
MT: Do what you love! We've come up with several business ideas that would have made money, but we just weren't into them all that much and couldn't get behind them. As you will be spending countless hours thinking about it, working on it, designing things for it, returning countless emails about it, redesigning things for it, dealing with unforeseen issues, and redesigning your redesigns, we repeat: you gotta love what you do. These are not complaints by any means; it feels great to overwork ourselves. And even though we've cut all communication with everyone in our lives aside from each other, turning an idea into an actual product is insanely rewarding.
Etchpop woodblocks.The second most important thing when starting a labor of love is to find a good accountant. Almost all businesses are the same when it comes to accounting and these head-shrinkingly boring meetings provide an essential foundation to build upon—which is much easier than trying to remodel the foundation after you've already started building. Forgive the cheesy metaphor but it’s true. It will save you time and money in the future.
Finally, use as many resources you can find, especially when they are free. Go to sba.gov and find a small business development center in your area. There is a lot of free/cheap help out there for people who want to start a new business. Try and find someone in your area that has the same type of machinery you are planning to buy or use, as they may be willing to talk to you, give you tips or suggestions or give you insights on how to get a better price on the machinery.
JR: Were there any aspects of starting Etchpop that were particularly difficult?
MT: One the most difficult parts has been realizing how much time everything actually takes to get done, if you want to have it done right, that is. We understand that our customers expect professionalism and coherency, so taking the extra thousand hours to perfect a process or idea is definitely worth the time. And although things are moving along somewhat smoothly, we still feel super lucky everyone has been so patient thus far.
JR: Anything else people should know?
MT: Etchpop.com is going live mid-April!
Prints made with an Etchpop woodblock.
-- John Ruscher